Engineering Plastics: Versatile Materials Shaping the Modern World
Engineering plastics are a class of materials that have revolutionized industries across the globe. These versatile polymers have found their way into numerous applications, offering an array of properties that make them indispensable in modern engineering and manufacturing. In this article, we will explore what engineering plastics are, their key characteristics, applications, and the advantages they bring to various sectors.
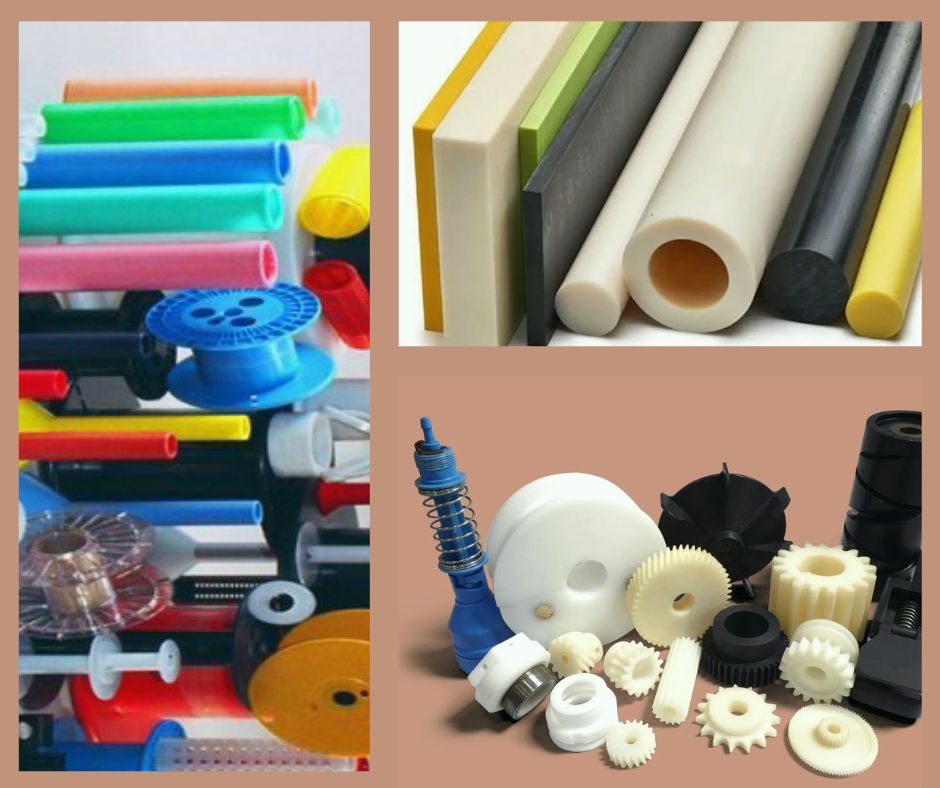
What Are Engineering Plastics?
Engineering plastics, also known as high-performance plastics or technical plastics, are a subset of polymers that possess enhanced mechanical, thermal, chemical, and electrical properties compared to commodity plastics like polyethylene or polypropylene. These materials are engineered to meet specific performance requirements, making them suitable for demanding applications in various industries.
Key Characteristics of Engineering Plastics:
- Mechanical Strength: Engineering plastics exhibit robust mechanical properties, including high tensile strength, impact resistance, and toughness. This makes them suitable for applications where structural integrity and durability are crucial.
- Thermal Stability: Many engineering plastics can withstand high temperatures without significant degradation. This property is vital in industries such as automotive, aerospace, and electronics, where components are exposed to heat stress.
- Chemical Resistance: These plastics are often resistant to chemicals, acids, and solvents, making them ideal for use in harsh environments, including chemical processing plants.
- Electrical Insulation: Engineering plastics often have excellent electrical insulating properties, making them valuable for electrical and electronic components.
- Low Friction: Some engineering plastics have low coefficients of friction, making them suitable for applications where reduced friction is essential, such as bearings and gears.
Applications of Engineering Plastics:
- Automotive Industry: Engineering plastics are extensively used in automobiles for various components, including engine parts, interior trim, and lightweight structural elements. Their durability, resistance to chemicals, and ability to reduce vehicle weight contribute to fuel efficiency.
- Aerospace: The aerospace industry relies on engineering plastics for lightweight yet durable components in aircraft and spacecraft. These materials help reduce fuel consumption and improve overall performance.
- Electronics: Engineering plastics serve as insulators and protective materials in electronic devices, ensuring electrical safety and thermal management.
- Medical Devices: They are used in medical equipment, where biocompatibility, sterilization resistance, and durability are critical factors.
- Consumer Goods: Engineering plastics are found in everyday items like appliances, sporting goods, and consumer electronics due to their versatility, aesthetics, and durability.
- Industrial Machinery: These plastics are used in various industrial equipment, including conveyor belts, gears, and seals, due to their wear resistance and ability to withstand harsh operating conditions.
Advantages of Engineering Plastics:
- Lightweight: Many engineering plastics offer a high strength-to-weight ratio, contributing to lightweight and fuel-efficient products.
- Durability: They have excellent wear resistance and can withstand prolonged use in demanding environments.
- Design Freedom: These materials can be molded into complex shapes, allowing for innovative product design.
- Cost-Efficiency: While initial material costs may be higher than commodity plastics, the longevity and performance of engineering plastics often result in cost savings over the product’s lifecycle.
- Environmental Benefits: The lightweight nature of engineering plastics can reduce energy consumption during transportation, contributing to lower carbon emissions.
Types of Engineering Plastics:
- There are several types of engineering plastics, each with its unique set of properties and applications. Some common types include:
- Polyamide (Nylon): Known for its excellent mechanical properties, including high tensile strength and impact resistance, nylon is widely used in gears, bearings, and automotive components.
- Polyethylene Terephthalate (PET): PET is often used in beverage bottles and food containers due to its transparency, good chemical resistance, and ease of processing.
- Polycarbonate (PC): PC is prized for its high impact resistance and optical clarity, making it ideal for applications like safety glasses, eyeglass lenses, and electronic display screens.
- Polyurethane (PU): PU is valued for its abrasion resistance and flexibility, making it suitable for products such as footwear, conveyor belts, and seals.
- Polyvinyl Chloride (PVC): PVC is known for its chemical resistance and electrical insulation properties. It is used in pipes, cable insulation, and vinyl flooring.
- Acrylonitrile Butadiene Styrene (ABS): ABS combines good impact resistance with the ability to be easily molded, making it a popular choice for consumer goods like toys, automotive trim, and
- Mechanical Properties: Engineering plastics offer a wide range of mechanical strengths, from rigid and strong materials like nylon to flexible and impact-resistant options like ABS.
- Thermal Properties: These plastics can maintain their structural integrity at elevated temperatures, with some variants capable of withstanding temperatures well above 100°C.
- Chemical Resistance: Many engineering plastics are highly resistant to chemicals, acids, and solvents, making them suitable for use in corrosive environments.
- Electrical Insulation: They often exhibit excellent electrical insulating properties, making them valuable for electrical and electronic applications.
- Low Friction: Some engineering plastics have low coefficients of friction, making them ideal for applications where reduced friction is essential.
- Specific Examples:
- Polyether Ether Ketone (PEEK): PEEK is a high-performance polymer with exceptional thermal stability, chemical resistance, and mechanical strength. It is commonly used in medical implants, aerospace components, and oil and gas applications.
- Polyimide (PI): PI is known for its high-temperature resistance and electrical insulation properties. It is used in flexible printed circuit boards (FPCBs), aerospace components, and electrical insulating materials.
- Polyphenylene Sulfide (PPS): PPS offers excellent chemical resistance and thermal stability, making it suitable for automotive parts, electrical connectors, and industrial components.
- Polyetherimide (PEI): PEI is known for its high-temperature resistance and dimensional stability. It is used in the aerospace, automotive, and electronics industries for applications requiring excellent mechanical and thermal properties.
Engineering plastics have become indispensable in modern engineering and manufacturing due to their exceptional properties and versatility. They play a vital role in a wide range of industries, from automotive and aerospace to electronics and medical devices. As technology continues to advance, we can expect even more innovative applications for these materials, shaping the future of various sectors while contributing to sustainability efforts through light weighting and improved efficiency. Read More About My Engineering Steel Hardox Plate
Comments are closed.