Engineering Plastics: PTFE vs. Nylon
Engineering plastics play a pivotal role in various industries due to their unique set of properties, offering durability, chemical resistance, and versatility. Two commonly used engineering plastics are Polytetrafluoroethylene (PTFE) and Nylon. This article will delve into the characteristics, applications, and differences between these two materials, aiding in selecting the appropriate one for specific engineering purposes.
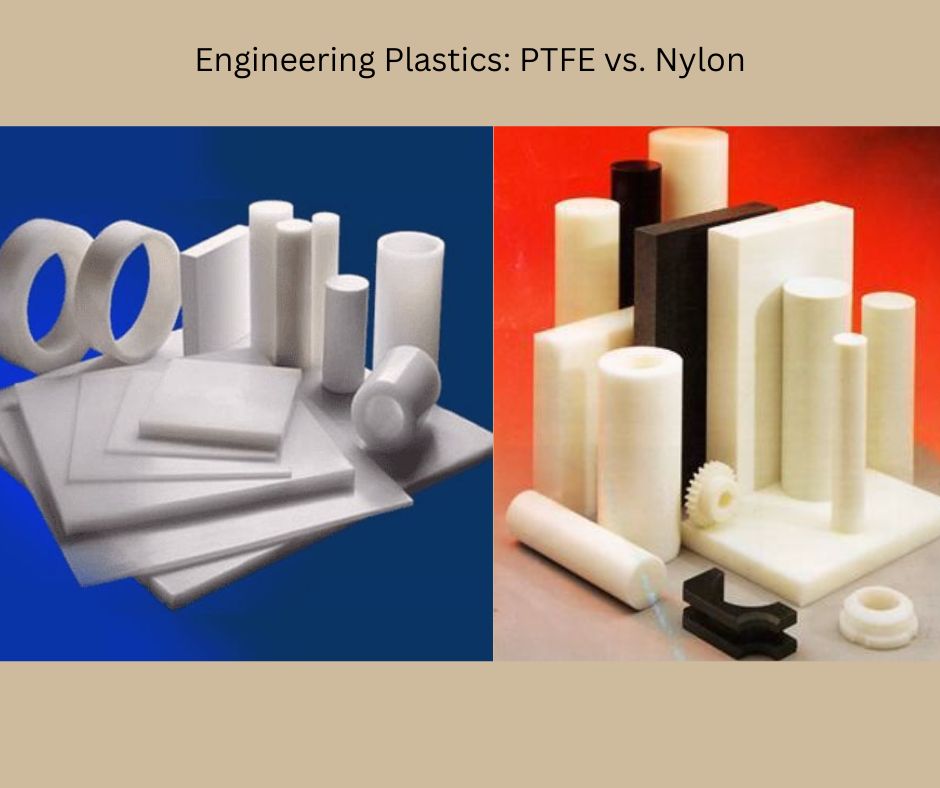
Polytetrafluoroethylene (PTFE):
1. Chemical Structure and Properties:
- PTFE is a synthetic fluoropolymer with a unique chemical structure composed of carbon and fluorine atoms. This structure gives it exceptional chemical inertness, making it highly resistant to acids, bases, and other corrosive substances.
- One of its most well-known properties is its extremely low coefficient of friction. PTFE is often referred to as the “slipperiest” material, making it an ideal choice for applications where reduced friction is crucial.
2. Applications:
- Chemical Industry: PTFE is widely used in the chemical industry due to its remarkable chemical resistance. It is employed for manufacturing gaskets, seals, and linings in equipment that handles highly corrosive chemicals.
- Food Processing: PTFE is a staple material in the food industry for non-stick cookware and components of food processing equipment. Its non-reactive nature ensures that it doesn’t contaminate food products.
- Electrical Industry: PTFE is valued for its high dielectric strength and is used as an insulating material in wiring, cable insulation, and electronic components.
3. Limitations:
- Mechanical Strength: PTFE has relatively low mechanical strength compared to some other engineering plastics, making it unsuitable for load-bearing applications.
- Wear Resistance: While PTFE is chemically inert, it has limited wear resistance compared to materials like nylon.
Nylon:
1. Chemical Structure and Properties:
- Nylon is a family of thermoplastic materials known for their toughness and versatility. The basic chemical structure of nylon includes repeating amide groups in its molecular chain.
- It possesses excellent mechanical properties, including high tensile strength and impact resistance.
2. Applications:
- Mechanical Engineering: Nylon is widely used in mechanical engineering applications. Its high mechanical strength and wear resistance make it suitable for producing gears, bearings, bushings, and other components subjected to high loads and friction.
- Automotive Industry: Nylon is employed in the automotive industry for various parts, including engine components, fasteners, and interior trims, thanks to its durability and versatility.
- Textile Industry: Nylon is used in the textile industry for clothing, fabrics, and industrial materials due to its strength and durability.
3. Limitations:
- Moisture Absorption: One limitation of nylon is its tendency to absorb moisture, which can lead to dimensional changes and altered mechanical properties. This should be considered in applications where moisture exposure is a concern.
- Chemical Resistance: While nylon exhibits good resistance to many chemicals, it is not as chemically inert as PTFE and may degrade when exposed to certain aggressive chemicals.
Comparison:
- Chemical Resistance: PTFE is unmatched in chemical resistance, while nylon may suffer degradation when exposed to specific chemicals.
- Mechanical Strength: Nylon excels in mechanical strength, making it suitable for load-bearing applications, whereas PTFE is not suitable for such applications due to its lower strength.
- Friction and Wear: PTFE’s low coefficient of friction is ideal for low-friction applications, while nylon is better suited for high-wear situations.
- Moisture Absorption: Nylon’s moisture absorption can affect its properties, while PTFE is hydrophobic and does not absorb moisture.
In summary, both PTFE and nylon are valuable engineering plastics, each with its own set of unique properties and applications. PTFE excels in chemical resistance and low-friction applications, whereas nylon shines in load-bearing and high-wear situations. The choice between them should be determined by the specific needs of the application, taking into consideration factors such as chemical exposure, mechanical stress, and friction requirements. Read More About it Engineering Plastics
Comments are closed.