Tool Steel: Exploring Grades, Characteristics, and Diverse Applications
Tool steel, a class of materials known for its remarkable strength, toughness, and wear resistance, holds a prominent place in various industries worldwide. Its versatility and ability to maintain its properties at high temperatures make it a crucial component in applications ranging from manufacturing to aerospace. In this article, we will delve into the characteristics of tool steel, explore different grades, and discuss its extensive applications in diverse fields.
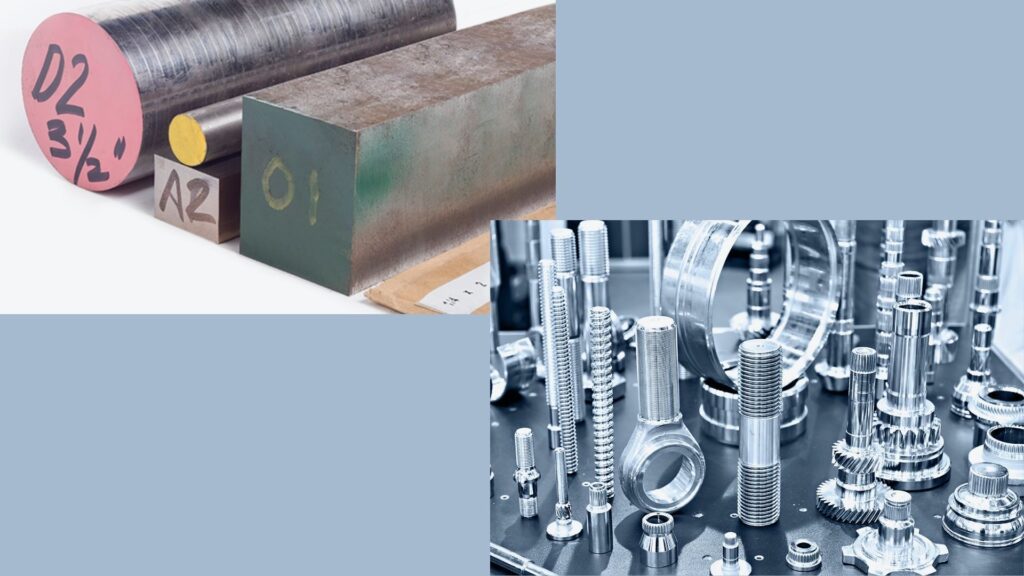
Characteristics of Tool Steel
- Hardness: Tool steel exhibits exceptional hardness, rendering it ideal for applications where cutting, shaping, and forming precision are paramount. It can maintain a sharp edge under substantial loads and high temperatures.
- Toughness: Despite its hardness, tool steel is characterized by excellent toughness, which helps prevent cracking and fracturing during demanding operations.
- Wear Resistance: Tool steel’s alloy composition gives it outstanding wear resistance, making it well-suited for cutting tools, dies, molds, and other applications involving repeated friction and abrasion.
- Heat Resistance: This material can operate efficiently at elevated temperatures without losing its mechanical properties, which is critical for high-speed machining and metal forming.
Types and Grades of Tool Steel
- Carbon Tool Steel: Primarily composed of carbon, this type of tool steel is commonly used for cutting tools, including drills and chisels. Its hardness is a notable feature, though it may lack the heat resistance of alloyed varieties.
- Alloy Tool Steel: Alloy tool steel incorporates additional elements such as chromium, molybdenum, vanadium, and tungsten to enhance its properties. Common subtypes include high-speed steel (HSS), hot work, and cold work steels.
- High-Speed Steel (HSS): Renowned for its ability to maintain hardness at high temperatures, HSS tool steel is used for applications like drill bits, saw blades, and high-speed cutting tools.
- Hot Work Steel: Designed for high-temperature applications like forging and die casting, hot work tool steel maintains its mechanical properties at elevated temperatures, resisting thermal fatigue and deformation.
- Cold Work Steel: Suited for operations at or near room temperature, cold work tool steel is used in applications such as stamping, blanking, and cold forming.
Applications of Tool Steel
- Cutting Tools: Tool steel is extensively used for cutting tools, including drills, end mills, and lathe tools, due to its hardness and exceptional wear resistance.
- Molds and Dies: In industries ranging from automotive to plastics, tool steel plays a vital role in the production of molds and dies for shaping and forming materials.
- Machine Components: Tool steel’s exceptional strength and durability make it a preferred choice for crafting machine components like gears, shafts, and bearings.
- Aerospace: Critical components in the aerospace industry, such as landing gear and turbine blades, often employ tool steel due to its strength and resistance to extreme conditions.
- Construction: Tool steel finds applications in construction, particularly for high-stress components like bridge pins and concrete formwork, where toughness and reliability are essential.
- Tool and Die Making: Tool steel is the foundation of tool and die making, serving as the material of choice for creating tools that manufacture countless products across various industries.
Weight Calculation Formula for Common Shapes
Calculating the weight of different shapes involves varying formulas based on the shape’s geometry. Here are the weight calculation formulas for some common shapes:
- Rectangular or Square Bar:Weight (in pounds) = Length (in inches) × Width (in inches) × Height (in inches) × Density (in pounds per cubic inch)The density varies depending on the material. For example, the density of mild steel is approximately 0.2836 pounds per cubic inch.
- Round Bar:Weight (in pounds) = π × (Radius in inches)^2 × Length (in inches) × Density (in pounds per cubic inch)
- Cylinder:Weight (in pounds) = π × (Radius in inches)^2 × Height (in inches) × Density (in pounds per cubic inch)
- Sheet or Plate:Weight (in pounds) = Length (in inches) × Width (in inches) × Thickness (in inches) × Density (in pounds per cubic inch)For thin sheets, you can approximate the thickness as the gauge (e.g., 18-gauge sheet).
Size Chart for Standard Steel Sections
Here’s a size chart for standard steel sections commonly used in construction and fabrication. Keep in mind that this is not an exhaustive list, and dimensions can vary depending on the specific standards and material grades.
I-Beams (American Standard):
- W4x13: 4 inches deep, 4.16 inches wide, 13 pounds per foot
- W6x9: 6 inches deep, 2.76 inches wide, 9 pounds per foot
- W8x18: 8 inches deep, 4.17 inches wide, 18 pounds per foot
- W10x30: 10 inches deep, 5.86 inches wide, 30 pounds per foot
H-Beams (American Standard):
- HP8x36: 8 inches deep, 5.31 inches wide, 36 pounds per foot
- HP10x42: 10 inches deep, 6.50 inches wide, 42 pounds per foot
- HP12x53: 12 inches deep, 7.99 inches wide, 53 pounds per foot
- HP14x73: 14 inches deep, 10.33 inches wide, 73 pounds per foot
Angle Iron:
- 2x2x1/4: 2 inches on each leg, 1/4-inch thickness
- 3x3x3/8: 3 inches on each leg, 3/8-inch thickness
- 4x4x1/2: 4 inches on each leg, 1/2-inch thickness
- 6x6x5/8: 6 inches on each leg, 5/8-inch thickness
Round Tubes (Outside Diameter x Wall Thickness):
- 1″ x 0.065″: 1-inch OD, 0.065-inch wall thickness
- 2″ x 0.120″: 2-inch OD, 0.120-inch wall thickness
- 3″ x 0.188″: 3-inch OD, 0.188-inch wall thickness
- 4″ x 0.250″: 4-inch OD, 0.250-inch wall thickness
Square Tubes (Outside Dimensions x Wall Thickness):
- 1″ x 1″ x 0.065″: 1-inch by 1-inch OD, 0.065-inch wall thickness
- 2″ x 2″ x 0.120″: 2-inch by 2-inch OD, 0.120-inch wall thickness
- 3″ x 3″ x 0.188″: 3-inch by 3-inch OD, 0.188-inch wall thickness
- 4″ x 4″ x 0.250″: 4-inch by 4-inch OD, 0.250-inch wall thickness
Please note that these dimensions and weights are provided as general examples and can vary based on regional standards and specific material types. When working with materials for a project, it’s essential to refer to the manufacturer’s specifications and standards to ensure accuracy. Additionally, materials like aluminum, copper, and plastics have different density values than steel, so you’ll need to adjust the weight calculation formula accordingly.
Tool steel’s unique blend of hardness, toughness, wear resistance, and heat resistance positions it as an indispensable material in modern industry and manufacturing. Its adaptability and reliability enable its use in a vast array of applications, from precision cutting tools to aerospace components and construction materials. As technology continues to advance, tool steel will remain a cornerstone in shaping the world around us.
Comments are closed.